Resources
Articles
What is Tar Impregnation -TI BRICK
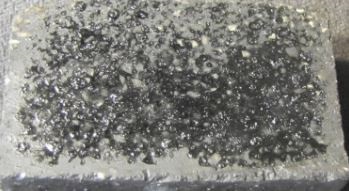
Tar, or pitch, impregnation is a process used to improve certain properties and/or provide protection to certain refractory products. The impregnation process involves forcing liquid pitch, at elevated temperatures, into the pores of the refractory products. This is done as a final process step, after the refractory has been formed and the bonding has been set by a heat processing. Generally this is done for fully fired/burned, ceramic bonded products, e.g. burned MgO.
Pitch is an organic distillation product, typically petroleum based, but coal tars are also used for refractory impregnation. Pitch is solid at room temperature, however for refractory impregnation, the pitch is typically maintained as a liquid at elevated temperatures (300-400F range); above the softening point of the pitch. Although specific process parameters vary
The following are the typical pitch impregnation process steps.
- The ‘white’ base refractory (to be impregnated) parts, are preheated just above the pitch temperature, generally in metal baskets.
- These preheated baskets are placed into an autoclave, which is then sealed.
- A vacuum is pulled on the autoclave. This removes much of the air within the pores of the refractory.
- The hot, liquid pitch is then introduced into autoclave covering the parts. Initially the vacuum helps to draw the liquid pitch into the internal portions of the refractory parts.
- The autoclave is pressurized and held at pressure for a set amount of time. Typical ceramic bonded refractory (i.e. relatively large pore size) parts are fully penetrated with pitch in a short amount of pressurized time (<1 hour).However thicker parts, and small pore size materials (i.e. C-Bonded refractory), require much longer dwells at pressure (5+ hours), and this may still not accomplish complete impregnation.
- The autoclave pressure is released and parts are removed from the autoclave.
- In most cases, impregnated parts then go through a secondary heat treatment step to partially carbonize the pitch, otherwise the pitch will simply bleed out when heat is applied in use. This step is generally referred to as tempering or ‘baking’. This is done under partially reducing conditions, which can simply involve sealing the pitch baskets in a metal cannister, minimizing oxygen during the process.
However, some processes will temper in a nitrogen atmosphere. Depending on the final application, and desired properties, tempering temperatures will vary from 650-1100ºF.
- For lower temperature applications, such as back-up and tank linings, lower tempering temperatures are used, which is often referred to as TIB (tar impregnated, baked).This will yield parts with increased volatiles, but given the lower service temperatures of the application, will not result in bleeding or smoking of parts in service.
- For higher temperature applications, such as steel contact, generally a TIHB process is used (tar impregnation, high bake).Although still not fully coked, the pitch still contains some low end volatiles, but not enough to cause bleeding or smoking during use.
- The objective of pitch impregnation is to fill the open porosity of the refractory. After the tempering process, the pitch filling the pores, become a partially carbonized structure within the refractory pores. This provides several benefits depending on the product and final application
- The reduced porosity and (partially) filled pores, reduces the degree of water and moisture penetration into the refractory. Thus pitch impregnation provides an increased level of hydration resistance for basic refractories.
- In liquid metal contact applications, pitch impregnation reduces penetration of slags, inclusion products, and the molten metal(s).Slag and inclusion components, will significantly alter the refractory by attacking the bonding phases, resulting in increased erosion and corrosion of the refractory. In addition, if thermal cycling is involved, the slag/steel penetrated refractory surface may spall off, during subsequent heat-up, due to a differential thermal expansion characteristics from the base (non-penetrated) refractory.
- The reduced porosity, and corresponding slight increase in density, increases the cold strength of the product. Depending on the application, these enhanced properties, will likely not contribute to the hot (in-service) strength of the refractory.
- Impregnated refractories have slightly better thermal conductivity, and improved thermal shock resistance as well. However, depending on the application, improvements in these properties may not provide noticeable refractory performance improvements.
Keep in mind, depending on the application, pitch may likely burn-out during use, which means any property improvements are temporary. However, even considering this, pitch impregnation often improves refractory life simply by delaying the onset of typical refractory wear mechanisms (i.e. erosion and corrosion); i.e. pitch impregnation “buys you additional heats, melts, life, etc.”.
Leave a comment
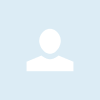
