Resources
Articles
Refractory Properties
Refractory properties are broken into mechanical physical properties and high-temperature properties. Typically, refractory materials are characterized by density, strength, and response to heat treatment. Certain physical properties are also measured and recorded during manufacture and serve as a basis for quality control.
Mechanical Physical Properties
- Bulk Density
- Apparent Porosity
- Modulus of rupture (flexural strength)
- Cold Crushing Strength (compressive strength)
High-Temperature Properties
- Permanent Linear Change (reheat test)
- Thermal Conductivity
- Linear Thermal Expansion
- Hot Modulus of Rupture (HMOR)
Mechanical Physical Properties for Refractory:
Physical properties address the mechanical attributes of refractory material, including the quantity needed for a furnace lining and strength. These properties relate to the expected service life and functionality. External factors play a large role, as the physical properties can change based on the conditions a refractory product is exposed to in service.
-
Bulk Density Related to Refractory:
Bulk density is a measure of the mass per volume. It is also the weight of the material required to fill a cavity of a defined volume. Density is often expressed in pounds per cubic foot using imperial units. Bulk density is also an important control property measured during the manufacture of a brick shape. For refractories based on alumina materials, density generally increases with alumina content. -
Apparent Porosity Related to Refractory:
Apparent porosity is a measurement of the volume of the open pores within a refractory. Since infiltrating materials from the process migrate through the pore structure, apparent porosity is a property to evaluate when selecting a refractory. Where there is a severe chemical attack or attack from slag, a lower porosity can increase resistance. -
Modulus of Rupture Related to Refractory:
Modulus of rupture (MOR) measures the flexural strength of a refractory. It is a key physical property. In the MOR test, a refractory is suspended across two points, and a force is applied between them. The force required to break a given cross-sectional area determines the modulus of rupture. In imperial units, the modulus of rupture is expressed as pounds per square inch (PSI). Modulus of rupture can be performed at elevated temperatures to determine its relative strength in service using the Hot Modulus of Rupture (HMOR) test. ASTM C-133 -
Cold Crushing Strength Related to Refractory:
Cold crushing strength measures the compressive strength of a refractory. The test is performed at room temperature after drying or firing. Refractories are ceramic materials and are stronger in compression than in tension. In the cold crushing strength test, the sample is broken between two flat surfaces. The force required to break the sample and the contact area of the sample is recorded, and the result is expressed in pounds per square inch. ASTM C-133 -
Abrasion Resistance Related to Refractory:
In many industrial applications, it is helpful to understand the resistance of refractory to an abrading medium. The standard test for abrasion resistance is ASTM C-704, originally developed for petroleum refinery applications. In this test, a weighed sample plate is exposed to a measured quantity of silicon carbide grit blown at standard pressure. After the abrading blast, the weight of the plate is measured again, and the loss of weight is expressed as a volume (cc loss) from the measured density. A low number indicates that it is more resistant. This test is conducted at room temperature.
High-Temperature Properties for Refractory:
While density, porosity, and most strength measurements take place at room temperature, a refractory’s service is at elevated temperature. High-temperature properties measure how it functions in service. Permanent linear change (reheat test) can predict its service temperature limit and how stable the material is at elevated temperatures. An important duty of refractory is insulation, and insulating value is measured as thermal conductivity. Linear thermal expansion measures how it grows or elongates as it is heated.
-
Permanent Linear Change (reheat test) Related to Refractory:
Early in the history of the refractory industry in North America, the reheat test was designed to measure the refractoriness, or temperature limit, of clays that were used to manufacture refractory brick. The permanent linear change (PLC) shows how it responds to heat treatment. The PLC test does not report reversible thermal expansion. This is measured by linear thermal expansion. The procedure for the test is to prepare a bar of the sample, measure the length of the dried bar before heat treatment, place the sample into a testing kiln held at the specified temperature (for example, 2910°F) for five hours, and then cool the sample back to room temperature. The new length is measured, and the change in length is reported as the PLC. Service temperature limits of refractory concretes are also defined using this test procedure. PLC is expressed in percentages (%). ASTM C-113 -
Linear Thermal Expansion Related to Refractory:
Unlike permanent linear change, linear thermal expansion measures the reversible thermal expansion. This test records the elongation of the material as it is heated. This is the property that is used to estimate whether it will require expansion allowance in an application. Linear thermal expansion is usually reported on a graph of % expansion vs. temperature. -
Thermal Conductivity Related to Refractory:
Thermal conductivity is a measurement of the refractory’s insulating ability. In imperial units, thermal conductivity is expressed in units referred to as the “k” factor, whose actual units are BTU-in/ft2- °F-hr. The K-factor is reported at various mean temperatures, which is the average temperature between the hot face surface and the cold face. ASTM specifies thermal conductivity methods in the United States. DIN specifies methods for European manufacturers. The values are not necessarily comparable between the two methods. Typically, C-201 or C1113. C-201 is the most accepted ASTM method. These methods give different results.
Refractory Properties Conclusion:
Each property is defined by a variety of testing methods. Testing methods must be consistent when comparing properties. The combination of properties and other factors, not simply just individual properties leads to extended service life. It's important to look at all properties, the installation methods, application, and environmental conditions when evaluating refractory properties. Avoid making decisions on refractories based on a single property as the lack/excess of another property might cause issues. Contact Resco Products technical staff to assist with making the right product selection.Leave a comment
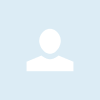
