Resources
Articles
Electric Arc Furnace Maintenance
Electric Arc Furnace Banks and Bottom Maintenance
Air or oxygen should be used to blow metal and/or slag out of holes in bottoms and banks. A minimum ¾” pipe with 100 psi capability is the customary standard for both. During blowing, furnaces may be tilted to facilitate draining.
Mechanical devices are not recommended in removing steel from holes since they tend to do too much damage to the refractory. Holes that are difficult to reach through the door may be noted and cleaned with oxygen after removal of the electric arc furnace roof.
Permanente 98-AF or Permanente 165-AF ram-cast mixes can be used for both cold and hot repairs. For cold repairs, the same quantity of water should be used for new bottom installation. For hot repairs, the mix should be made just wet enough so that it will not stick to the shovel when shoveling the mix into the furnace. Any tendency for the material to stick to the shovel may be eliminated by dipping the shovel into clean water before each shovelful. Another commonly used method of preventing sticking is that of thrusting the shovel into a pile of raw dolomite.
Use drinking water for mixing. Never use water from the furnace cooling system. Water additives for demineralizing will adversely affect the patented bonding agents in Permanente ram-cast materials.
The total amount of Permanente mix needed for the patch should be placed in the hole as rapidly as possible. If the patch is not too large, the entire amount should be mixed at one time.
A revolving blade-type mixer, similar to a mortar mixer, is recommended for patching. Mixing on the floor can be done if care is exercised to prevent dirt, dolomite, or other materials from being mixed into the batch.
Electric Arc Furnace Emergency Patch on the Lower Sidewalls
A hole in the lower sidewall with sufficient brick thickness around it may be patched as follows: place a piece of sheet iron between the scrap and the hole on the first charge. Mix Permanente 98-AF or Permanente 165-AF with about 12% water and shovel it into the hole from a position on the bezel ring of the furnace.
When the application of the mix has been completed, press the sheet-iron against the patch, and wedge the scrap behind it to hold it in place. Usually, the patch will be in place after the heat is tapped and should last for a good number of heats. This practice is successful in most instances, and we believe it well worth trying before shutting down a furnace because of such a hole in the lower sidewall.
Piping Tap Holes During Electric Furnace Campaign
The pipe is set at the correct slope and elevation from the outside of the furnace by placing wet Permanente 98-AF or 165-AF under it. If it is necessary to lower the tap hole before introduction the pipe, this can be accomplished by the oxygen lance or by sledging steel and slag out with a bar. Try to remove all the steel possible. Then smooth wet Permanente 98-AF or 165-AF on the tap hole bottom and set the pipe. The entire pipe should rest on the mix. Pipe length should be enough to reach from the inside brick face to the outside of the shell. Refractory material may be applied either manually or gunned.
The major portion of the manual work done on a hot furnace is accomplished from the back of the furnace. Wet Permanente 165-AF is applied by hand and with steel spatulas to the space between the old tap hole and pipe, as far into the tap hole as possible. The material should be well packed; filling all voids around the pipe.
Dolomite is then shoveled into the furnace to cover the inner tap hole face and pipe. If it has been impossible to fill the opening between the pipe and the old tap hole from the outside, dead-burned dolomite or magnesite is shoveled into the furnace to fill the remaining opening from the inside.
Leave a comment
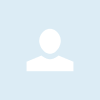
