Rotary Kiln Charging Zone Refractory Challenges
Articles
Surveying the non-captive lime industry reveals there are approximately 120 rotary kilns producing pebble lime in the US. Just over half of these rotary kilns have stone preheaters that substantially improve their fuel efficiency. Rotary pebble lime kilns typically have four refractory zones: charging, calcining, burning, and discharge.
Part 2: Calcining Zone
Part 3: Burning Zone
Part 4: Discharge Zone
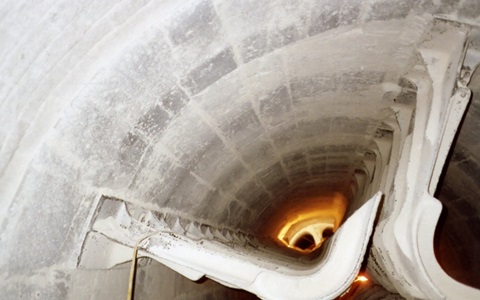
Rotary lime kilns have four refractory zones: discharge, burning, calcining, and charging.
A highly abrasion-resistant R-MAX© C lining in a metallic heat exchanger section of a long pebble limestone kiln still shows the form marks after 16 months of service.
Charging Zone Refractories
Conditions that the refractory must withstand in the charging zone vary with the process type. In preheater kilns, the stone feed can be partially calcined as it falls through the transfer chute into the rotary kiln. Partial calcination softens the abrasiveness of the feed: and high alumina brick with moderate abrasion resistance, including burned 70% alumina brick, can withstand the moderate abrasion.
Long rotary kilns without preheaters require abrasion-resistant refractory in the charging zone, where abrasion of the stone can be particularly severe. Typically, phosphate-bonded high alumina refractory brick lines the charging zone. Phosphate-bonded brick exhibits high-strength, and outstanding abrasion resistance.
The standard refractory test in North America for abrasion resistance is the ASTM C-704 procedure. In this test, specially sized silicon carbide grit is blasted onto a weighted refractory specimen at 90° angle. The volume loss from the scouring abrasion is calculated from the loss in weight of the sample and reported in cc’s. Thus, a smaller volume loss indicates better abrasion resistance. Typically, abrasion loss for 70% alumina brick is approximately 8 to 10 cc loss, while phosphate-bonded 80% alumina brick shows less than 4cc loss.
Long pebble lime kilns may have internal devices to facilitate heat exchange, like metallic lifters in the feed, ends. In such cases, the installation of refractory brickwork between the heat exchangers can be time-consuming, and a monolithic refractory is more suited, so as to reduce installation time. For such applications, a special abrasion-resistant monolithic refractory was developed to solve abrasion problems.
This monolithic refractory uses advanced particle packing and a special bonding matrix to achieve exceptional strength and abrasion resistance. The family name is R-MAX©, and R-MAX© castable can exhibit abrasion losses of less than 3.0 cc after heating to 816°C(1500°F) in the ASTM C-704 test. R-MAX© castable comes in a variety of consistencies, depending on the intended use, including versions for pneumatic gunning. In one cast installation between metallic heat exchangers in a long kiln feed end, the performance R-MAX© C (casting grade) surpassed the wear resistance of other low-cement castable used previously (Figure 2). R-MAX© castable has been widely used in many other lime kiln applications, including transfer chute and preheater linings.